A Magyar Épületgépészek Szövetségének Ipari-technológiai Tagozata, az Épületgépészeti Hegesztési és Technológiai Klaszter, valamint a REHAU Kft. közös szervezésében gyárlátogatással egybekötött Ipari-technológiai szakmai napot tartottunk Győrben.
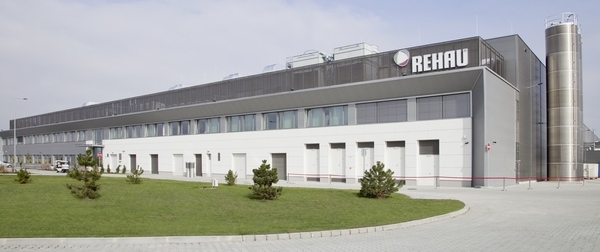
A program a REHAU Automotive Kft. győri gyárában indult, ahol Pánger László, a Magyar Épületgépészek Szövetsége Ipari-technológiai Tagozatának vezetője és Kugler Géza, a Rehau Kft. vezető tanácsadója köszöntötte a megjelent ötven épületgépész tervező és kivitelező szakembert.
Ezután Lászlófi András, a REHAU Forgalmazó Kft. mérnök tanácsadója szakmai előadást tartott a cég hő- és anyagtranszportot biztosító csővezeték rendszereiről. Rövid áttekintést adott a német családi vállalkozásként alapított, ma már világméretű vállalatról, mely három stratégiai területen (építőipar, autóipar, ipar) van jelen a világban. Magyarországon két városban található irodájuk, Biatorbágyon, illetve Győrben, ahol az első magyar gyár is épült. Itt jelenleg kizárólag az Audi részére folyik a lőkhárítók gyártása, de a későbbiekben tervezik más autómárkák számára is a termelést. Lászlófi András érdekességként elmondta, hogy minden harmadik Európában gyártott autó rendszermegoldásait a REHAU szállítja, és világszerte több mint 235 stadion sportpályáján használják a cég termékeit. Az autóipar mellett a vállalat másik nagy stratégiai területe az ipari csővezeték rendszerek. A REHAU csőrendszereit használják ipari közegek szállítására, ipari fűtés és hűtés területén, élelmiszerek szállítására, illetve a vezetékes távfűtés területén is. A cég összes csővezetéke PE-Xa (peroxidos térhálósítás) eljárással készül, ami jobb, mint az utólagosan történő térhálósítás. Az előadáson ismertették a kötéstechnikai eljárásokat, és beszéltek a csövek hőszigeteléséről is. Elmondták, hogy a műanyagcsöveknél nagyon fontos a hőtágulásból adódó problémák megoldása. Ezzel kapcsolatban egy kisfilmet is megtekintettünk, ami a pécsi főiskolán létrehozott mintaprojektről készült, és a fűtés/hűtés során a RAUPEX ipari csővezetékekben jelentkező hőtágulást szemlélteti.
/MEGJEGYZÉS: A fenti előadást meghallgathatják az érdeklődők november 28-án is, az Épületgépészek Napjának keretében szervezett kötelező mérnök kamarai továbbképzésen, melynek témája az ipari épületek épületgépészete. Bővebb információk ITT /
Az előadást követően szervezett busszal mentünk át a negyedórányira lévő Audiba. Itt két csoportban, szakszerű idegenvezetéssel, a látogatói szabályok megismerése után indultunk el. Az Audi 1993 végén kezdte meg működését Magyarországon először motorgyártással (előszéria), majd 1994-ben megnyitotta a győri motorgyárat. Ma az Audi teljes motorválasztéka innen származik, de szállít a Volkswagen, a Seat és a Skoda márkák számára is. Az évek során a folyamatos bővítések egyik legjelentősebb állomása az volt, amikor 2005-ben megnyílt a szerszámüzem, amely szállít szerszámokat a présüzemnek, és készülékeket a karosszériaüzemnek is. A gyár tevékenységi területe 4 csoportba osztható: motorgyártás; szerszámgépgyártás; járműgyártás és motorfejlesztés és –tesztelés (ami 2011-ben a járműfejlesztéssel bővült). 2013-ban nyílt meg a teljes gyártási folyamatot lefedő járműgyár Győrben, melynek részei a présüzem, a karosszériaüzem, a lakkozó és a szerelde. Jelenleg több mint kétmillió négyzetméter területen 11.200 dolgozót foglalkoztatnak 3 műszakos munkarendben vasárnap estétől szombat reggelig. Először az új Audi A3 Limousine, majd októbertől az új A3 Cabriolet sorozatgyártása indult meg, ezután jött az Audi TT Coupé és a Roadster. Ez év nyarán kezdték meg a TT harmadik generációjának gyártását, mely jelenleg még nincs kereskedelmi forgalomban, így a gyártási folyamat bizonyos részei titkosítva vannak. Mi is csak a présüzemet és a karosszériaüzemet nézhettük meg, a szerelde csak 2015. januárjától lesz látogatható. A présüzemben kezdődik a komplett járműgyártás, amihez az alapanyagot (tekercseket) Dorogról szállítják. Az üzemben a legmodernebb, energia-visszanyerős technikákat alkalmazzák, mindössze 160 embert foglalkoztatnak. A préselemeket híddarukkal mozgatják, melyek 66,5 tonna terhelhetőségűek. Mivel a présszerszámok nagyon nehezek, speciális teherbírású padló kialakítására is szükség volt, melyet 24 nagy acélrugó tart alulról. A munkadarab préselés után a karosszériaüzembe kerül, ahol különböző hegesztési eljárásokkal illesztik össze az elemeket. Ez az üzemrész 950 munkatársat foglalkoztat. A teljes karosszéria 2 óra alatt készül el, az elemeket ultrahangos technikával ellenőrzik, ami még a hajszálrepedéseket is kimutatja. A precizitást és a minőséget mutatja, hogy a gyártási adatokat 25 évig megőrzik, így bármely hiba esetén visszakereshető a gyártási folyamat. Érdekes volt még, hogy az egyes elemeket vágányon szállítják az üzemek területén, a teljes gyárban összesen 12 km vágány található. A kész autók csomagoltan kerülnek a parkolóba, ahonnan folyamatosan szállítják el őket a megrendelőkhöz. Az Audi minden autót megrendelésre, egyedi igények szerint összeállított felszereltséggel gyárt.
Az Audi gyár látogatása után visszatértünk a REHAU gyárba, ahol megebédeltünk, majd két előadás következett.
Először Csapó Balázs, a REHAU Automotive Kft. munkatársa röviden bemutatta a győri gyárat, ahol az Audi részére folyik a lökhárítók gyártása. Elmondta, hogy kb. 2 percenként jön le egy termék a gyártósorról, csakúgy mint az Audiban, ahol szintén két percenként gördül le egy autó a gyártósorról. Vagyis a két gyár termelése teljes szinkronban van, így biztosítva a folyamatos szállítást. Ismertette, hogy a látogatás során milyen szabályokat kell betartanunk, illetve hogy pontosan mit és milyen sorrendben fogunk megnézni.
Ezt követően Keresztes-Nagy Zsolt, a KAESER Kompressoren mérnök-üzletkötője tartott előadást a sűrített levegő technikáról. A téma szorosan kapcsolódott a szakmai nap programjához, hiszen a REHAU gyár részét képezi egy Kaeser kompresszorház is, melyet a nap végén szintén megtekintettünk. Előadásában elmondta, hogy az iskolákban nem tanítják ezt a technikát, pedig a sűrített levegő minden gyártóüzem fontos eleme. Ismertette a sűrített levegő előállítását, előkészítését (melynek során szűrik nedvességre, porra és olajra), energetikai előnyeit és a lényegesebb tervezési alapelveket. Bemutatta az 1919-ben alapított bajor céget, és annak fontosabb fejlődési mérföldköveit. A sűrített levegő előállítás és előkészítés technikai részletezésén túl ismertette a sűrített levegőre vonatkozó ISO8573-1 szabvány legfontosabb ismérveit és a tervezők, illetve felhasználók szempontjából alapvető és hasznos tudnivalókat. Elmondta azt is, hogy a sűrített levegő a legköltségesebb energiaforrás, így annak előállítása minden azt használó cégnek komoly ráfordítást igényel. Azonban e ráfordítás mértéke alapvetően a levegőt előállító rendszer fajlagos-teljesítményének függvénye. Ezzel kapcsolatban bemutatta a Kaeser rendszerek energetikai előnyeit.
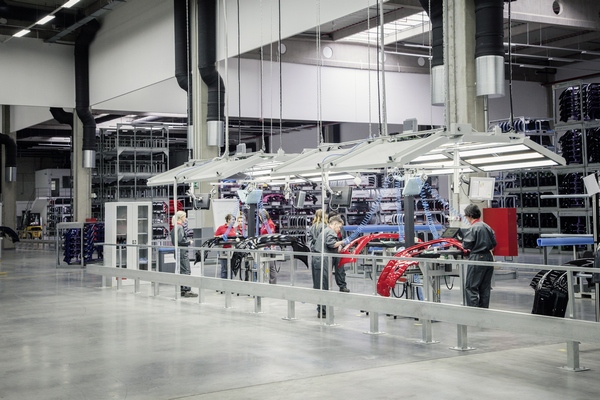
A nap végén megtekintettük a 2013. október 14-én megnyílt REHAU gyárat. Az átadást megelőzően is, már 2005 óta szereltek lökhárítókat az Audi részére, de akkor még csak bérelt telephelyen működve. Az új gyár tervezésénél nagy figyelmet fordítottak az energiahatékony üzemelésre és a megújuló energiák felhasználására. A gyárban a termelés, az Audihoz hasonlóan folyamatosan, 3 műszakban zajlik. Első lépésként műanyag granulátumból fröccsöntéssel előállítják a lökhárítókat. Az öntés 5000 ºC-on történik, majd a formafelvételt követően megkezdődik a hűtés. Az elemek 60 ºC-on hagyják el a gyártósort, majd további hűtést követően, a termelés második fázisaként a lakkozócsarnokba kerülnek. Itt nagyon fontos az állandó hőmérséklet (22 ºC) és a tisztaság, hiszen bármelyik hiánya a termék magas minőségét veszélyezteti. A festési folyamat a tisztítással kezdődik, aztán jön az alapozó lakk felvitele, majd az Audi megrendelése szerinti színnel következik a festés. A géppark legfontosabb eleme a REHAU fejlesztése, a moduláris rendszerű CO2 gázzal üzemelő tisztítógépet alkalmazó lakkozó berendezés. A termelés harmadik fázisaként az összeszerelés következik, melyhez az egyéb elemeket (pl: lámpabúra) nem itt helyben gyártják, hanem beszállított késztermékként érkezik. A folyamatot az ellenőrzés zárja, melynek során a gyártott elemekből minden nap kb. 3 elemet szúrópróbaszerűen kiemelnek, és ezeket utólagosan alapos méréseknek vetik alá.
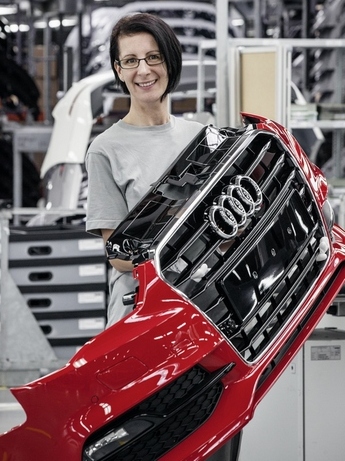
A szakmai napot a Kaeser kompresszorház megtekintése zárta, ahol a korábbi előadásban halottakat és a rendszer részeit a valóságban is megfigyelhettük.
Az előadások címére kattintva letöltheti azok anyagát:
(Figyelem! Előfordulhat, hogy megnyitáskor szétcsúszva jelenik meg az anyag a Firefox böngésző pdf megjelenítője miatt. Ilyen esetben kérjük, töltse le számítógépére a pdf-et, mert saját gépről megnyitva már hibátlanul jelenik meg az előadás!)
REHAU általános rendszerek, különleges alkalmazások Hő- és anyagtranszportot biztosító csővezeték rendszerek Lászlófi András, mérnök tanácsadó, Rehau Forgalmazó Kft.
KAESER Kompressoren - A minősített sűrített levegő technika Keresztes-Nagy Zsolt, mérnök-üzletkötő, Kaeser Kft.
|